Manufacturing Management System
The manufacturing department is one of the important departments in industrial establishments of all kinds and requires specific tools to manage their work professionally. The system has a flexible professional cycle that helps achieve integration between manufacturing management, accounts and inventory, and this is evident through the following tools:
Material table:
Through the table of materials, the final product, the raw materials needed for its production, and the quantities are determined, in addition to any other manufacturing expenses on the product such as workers’ wages, the cost of rent, electricity and any other costs
production order:
Through the production order, we can issue orders to produce specific quantities, through which the system withdraws the quantities of raw materials previously defined on the table of materials from the raw materials warehouse to the specified manufacturing warehouse
After withdrawing the materials, the production order appears in the process, and after manufacturing is completed, we press the Finish button, which in turn performs the work of withdrawing the finished materials from the workstation warehouse to the finished materials warehouse. The production order can be partially finished, meaning issuing a production order of 100 units and returning the finished materials in Partially according to the quantity produced
Production planning tool:
This tool is concerned by collecting multiple sales orders in one production order, this feature is ideal, especially for companies that are interested in operating production machines to produce a minimum number of items, for example some machines are only operated to produce 1000 units of the item as a minimum, due to the costs of high operating
Manufacturing reports:
Open Manufacturing Orders Report: This report provides details of the manufacturing orders in progress and tracks completed and working quantities with the ability to follow the planned time to completion of production
Finished production orders report: a report that shows finished production orders during a specified period of time
Production Analysis Report: This report is concerned with production processes by following them through the different stages of production, as it reflects the production quantity of production orders that have not yet started as well as production orders in progress and the quantities of production orders already produced
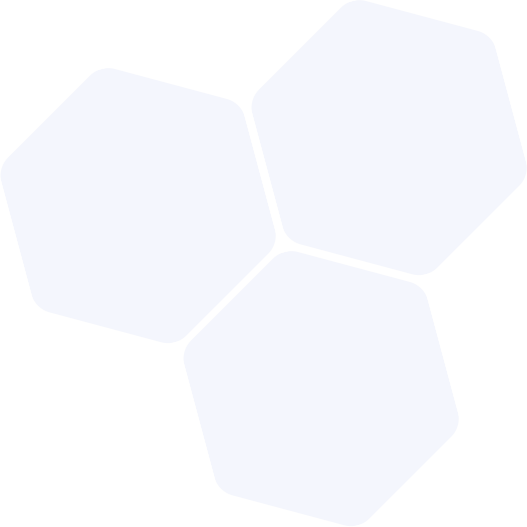